Unlocking Innovation: The Power of Rapid Prototype Injection Molds
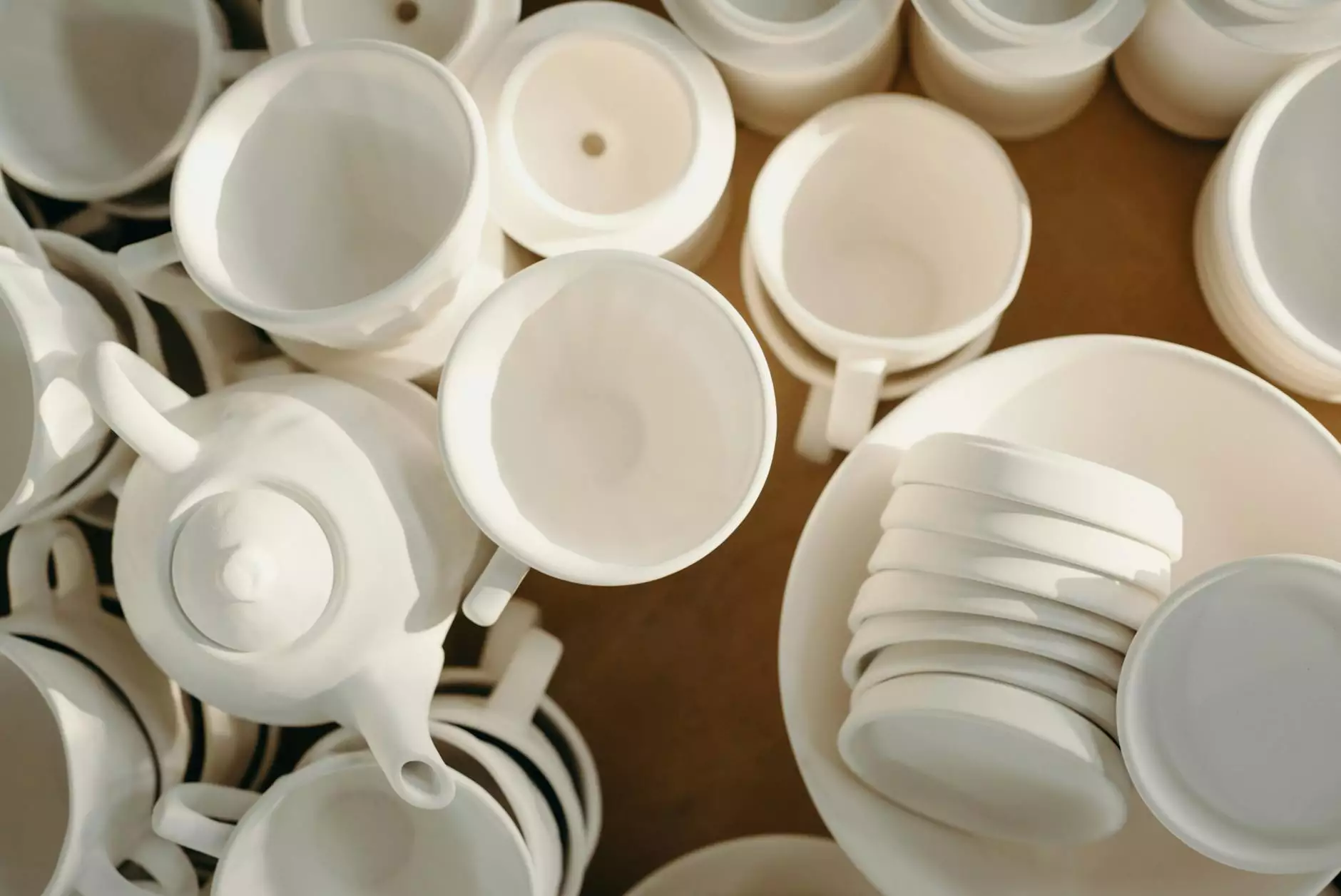
In today's dynamic business environment, the ability to design and manufacture products quickly and efficiently is crucial for success. Among the revolutionary tools in modern manufacturing, rapid prototype injection molds stand out as a game changer, especially in sectors that require high precision and speed, such as metal fabrication. In this article, we will explore what rapid prototype injection molds are, their benefits, applications, and the future of this innovative technology.
Understanding Rapid Prototype Injection Molds
Rapid prototype injection molding refers to a technique used to create prototypes quickly using injection molding processes. It combines advanced materials with cutting-edge technology to produce high-quality, functional prototypes in a fraction of the time and cost traditionally associated with conventional manufacturing methods.
How Rapid Prototype Injection Molds Work
The process involves several key steps:
- Design Phase: The initial product concept is developed using CAD (Computer-Aided Design) software. This allows for precise modeling of the part.
- 3D Printing: The design is often validated through 3D printing, which allows for quick iterations and adjustments before moving to the molding stage.
- Mold Creation: Once the design is finalized, a mold is created—typically made from steel or aluminum—that can withstand the injection process.
- Material Injection: The selected plastic material is injected into the mold under high pressure.
- Curing & Cooling: The material is allowed to cure before being cooled, which solidifies the prototype into its final form.
- Post-Processing: After removal from the mold, the prototype may undergo finishing processes such as sanding or painting.
Benefits of using Rapid Prototype Injection Molds
The value of implementing rapid prototype injection molds cannot be overstated. Here are some of the most significant benefits they offer:
1. Speed to Market
One of the most substantial advantages is the remarkable reduction in development time. Traditional manufacturing methods can take weeks or even months to produce prototypes, whereas rapid prototyping can yield results in days. This accelerated timeline enables businesses to launch products faster and stay ahead of their competition.
2. Cost Efficiency
By utilizing rapid injection molding, companies can significantly cut down on costs associated with material waste and labor. Traditional prototyping methods often involve expensive tooling processes, which are minimized through rapid prototyping technologies. Thus, businesses can invest their resources more strategically.
3. Quality and Precision
Rapid prototypes produced via injection molding are known for their high dimensional accuracy and surface finish. This allows for prototypes that are not only functional but also visually representative of the final product, making it easier to conduct tests and validations.
4. Flexibility in Design
The ability to quickly revise designs based on feedback is paramount in product development. With rapid prototype injection molds, modifications can be made on the fly, allowing teams to iterate swiftly and efficiently.
5. Enhanced Collaboration
The rapid production of prototypes fosters better communication and collaboration among team members. Having a tangible product to review facilitates more effective discussions around design, function, and market readiness.
Applications of Rapid Prototype Injection Molds in Metal Fabrication
Rapid prototype injection molds have a wide range of applications, particularly in the metal fabrication industry. Here are some key areas where this technology is making a significant impact:
1. Automotive Industry
The automotive sector is continuously evolving, and rapid prototyping plays a crucial role in the development of new vehicle parts. With rapid prototype injection molds, manufacturers can create and test components, leading to improved safety features and enhanced performance.
2. Aerospace Engineering
In the aerospace field, precision is non-negotiable. Rapid prototyping allows engineers to produce critical components while ensuring high standards of quality and performance. This is essential for maintaining safety and adherence to strict regulations.
3. Consumer Electronics
The fast-paced world of consumer electronics demands constant innovation. Rapid prototyping facilitates quick turnarounds in product design, enabling companies to meet consumer expectations for cutting-edge features and sleek designs without compromising on quality.
4. Medical Devices
The medical device industry requires prototypes for testing and regulatory approval. Rapid prototype injection molding allows for the swift development of devices, ensuring they meet stringent health and safety standards while being brought to market quickly.
The Future of Rapid Prototype Injection Molds
As technology continues to evolve, the future of rapid prototype injection molds looks promising. Innovations such as smart materials that adapt to their environment and enhanced 3D printing techniques are set to revolutionize the manufacturing landscape even further.
1. Integration with AI and Machine Learning
The incorporation of AI in the design and prototyping phases will streamline processes, allowing for enhanced accuracy and customization. Predictive analytics can forecast potential design flaws early in the process, saving time and resources.
2. Sustainable Manufacturing
Eco-friendliness is becoming increasingly important in manufacturing. Future developments in rapid prototype injection molds are expected to focus on minimizing waste and using biodegradable materials, aligning production processes with sustainability goals.
3. Expanded Material Options
Ongoing research into different materials will widen the range of applications for rapid injection molding. This means that more industries will benefit from the speed and efficiency of this technology, leading to greater innovation.
Conclusion: Embracing the Future with Rapid Prototype Injection Molds
In summary, the significance of rapid prototype injection molds in today's manufacturing landscape cannot be overstated. By providing unprecedented speed, cost savings, and quality, they are becoming essential tools in various industries, including metal fabrication. Companies like DeepMould.net are at the forefront of this revolution, ensuring that businesses can keep pace with consumer demands and technological advances.
As we forge ahead, the continued evolution of rapid prototyping will unlock even more opportunities for innovation, allowing businesses to thrive in an increasingly competitive marketplace. By leveraging these technologies, manufacturers can not only meet the demands of today but also pioneer the products of tomorrow.