Understanding Auto Mould: Pioneering Innovation in Metal Fabrication
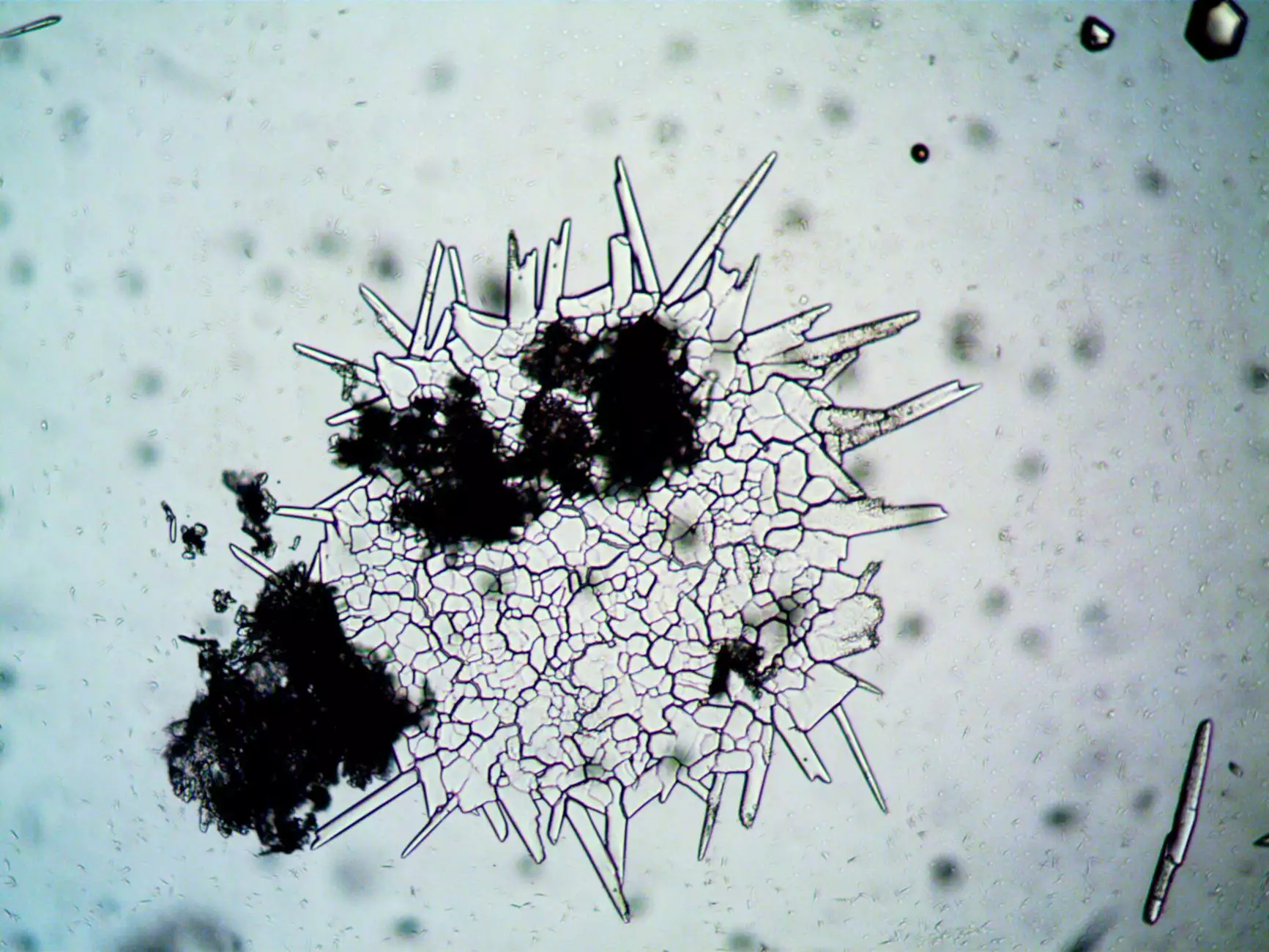
Auto mould technology plays a crucial role in the metal fabrication industry, offering unparalleled precision and efficiency in manufacturing processes. As a key component in the production of automotive parts, the importance of moulds in achieving high-quality outputs cannot be overstated. This article will delve into the nuances of auto mould, its applications, benefits, and how it contributes to the evolving landscape of metal fabrication.
The Importance of Moulding in Metal Fabrication
In the world of manufacturing, the term “moulding” refers to the process of shaping materials into specific forms. Within the realm of metal fabrication, the auto mould serves as the backbone for producing components that meet stringent specifications.
What is an Auto Mould?
At its core, an auto mould is a specially designed tool used to shape molten metal into predefined geometries. These moulds are predominantly utilized in the automotive industry, where precision and durability are paramount. The process involves:
- Heating metal materials to their melting point.
- Pouring the molten metal into the pre-designed mould cavity.
- Allowing the metal to cool and solidify, taking the shape of the mould.
Applications of Auto Mould in the Automotive Sector
The applications of auto mould technology are extensive. It is employed in producing a variety of components, including:
- Engine Blocks: The core of every automobile engine, essential for performance.
- Transmission Housings: Crucial for protecting and housing vehicle transmissions.
- Suspension Components: Important for vehicle stability and control.
- Body Panels: Aesthetic and structural components of the vehicle's exterior.
The Benefits of Using Auto Mould
The adoption of auto mould technology offers several advantages:
1. Precision Engineering
Auto moulds provide an exceptional level of accuracy in the production of complex shapes. This precision reduces the need for extensive machining post-production, which can save both time and material costs.
2. Cost Efficiency
Investing in auto mould technology can lead to significant cost reductions in the manufacturing process. With lower waste rates and higher production speeds, businesses can optimize their profitability.
3. Enhanced Durability
Components produced using high-quality moulds tend to offer improved durability and performance. This is particularly critical in the automotive industry where safety and reliability are non-negotiable.
Innovations in Auto Mould Technology
As the automotive industry continues to evolve, so too does the technology behind auto mould manufacturing. Some recent innovations include:
1. 3D Printing
3D printing technology has begun to influence the way auto moulds are created. Rapid prototyping allows for faster iterations and design improvements, which can significantly reduce lead times in production.
2. Smart Moulding Techniques
Integrating IoT (Internet of Things) into moulding processes allows for real-time monitoring and adjustments, enhancing efficiency and reducing errors.
Choosing the Right Auto Mould Supplier
When it comes to selecting a supplier for auto mould services, it is vital to consider several factors:
1. Industry Experience
Look for suppliers with a proven track record in the automotive sector. Their experience will be invaluable in navigating the specific challenges of your project.
2. Quality Assurance
Ensure that the supplier adheres to strict quality control measures. Certifications such as ISO9001 can be indicators of a commitment to quality.
3. Technological Capabilities
Evaluate the technological resources the supplier offers. Advanced machinery and innovative processes can greatly affect the end quality of the auto mould products.
Case Studies: Success Stories of Auto Mould Implementation
To illustrate the effectiveness of auto mould technology, let's explore some successful implementations in the automotive industry:
Case Study 1: Streamlining Production at XYZ Motors
XYZ Motors faced challenges in meeting production targets due to inefficiencies in their mould-making process. By partnering with deepmould.net, they adopted robust auto mould technology which led to:
- A 30% reduction in production time.
- 20% lower material waste.
- Significantly improved part consistency and quality.
Case Study 2: Enhancing Performance at ABC Automotive
ABC Automotive sought to improve the performance of their vehicle components. Through advanced auto mould techniques, they achieved:
- Enhanced durability of engine components.
- Cost savings through reduced machining requirements.
- Faster time-to-market for new vehicle models.
The Future of Auto Mould in Metal Fabrication
The future of auto mould technology in metal fabrication is poised for growth. As manufacturers continue to push the boundaries of innovation, we can expect:
1. Greater Sustainability
There is an increasing demand for sustainable practices within the automotive industry. The development of eco-friendly materials and processes in auto moulding will be critical in reducing environmental impacts.
2. Increased Automation
Automation will become more prevalent, leading to enhanced precision and efficiency in the moulding process. This shift will help manufacturers meet the growing demand for high-quality automotive products.
Conclusion
In conclusion, auto mould technology is an indispensable element of the metal fabrication sector, particularly in the automotive industry. Its numerous applications, coupled with the technological advancements in mouldmaking, are set to reshape the future of manufacturing. Companies like deepmould.net are at the forefront of this evolution, driving innovation and excellence.
By understanding the intricacies of auto mould, businesses can harness its potential to enhance production efficiency, reduce costs, and improve product quality, ultimately leading to greater success in the competitive automotive market.